1. 内部応力とは何か
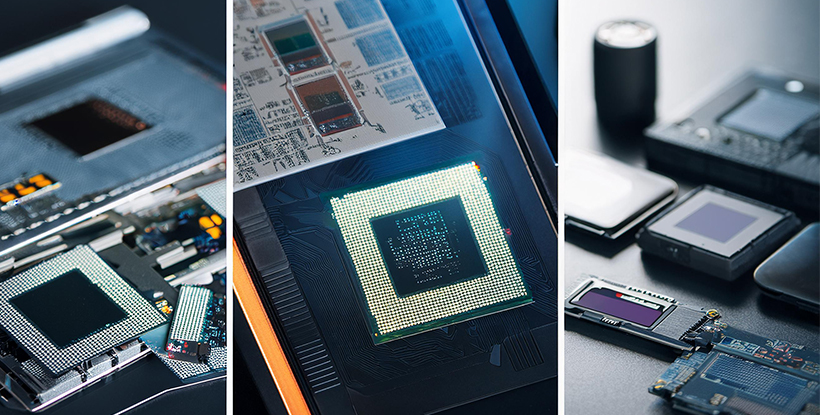
内部応力とは、材料の内部で発生する余分な力やひずみを指します。これは、温度変化や不適切な設計、製造プロセスの不備などが原因で発生します。SMTの製造過程では、プリント基板(PCB)や実装部品の接合部分、さらにはリフロー工程での温度変化によって、材料内部に応力が蓄積されることがあります。この応力が放置されると、クラックの発生や接合部の劣化、長期的な信頼性の低下につながる可能性があります。
2. 発生原因
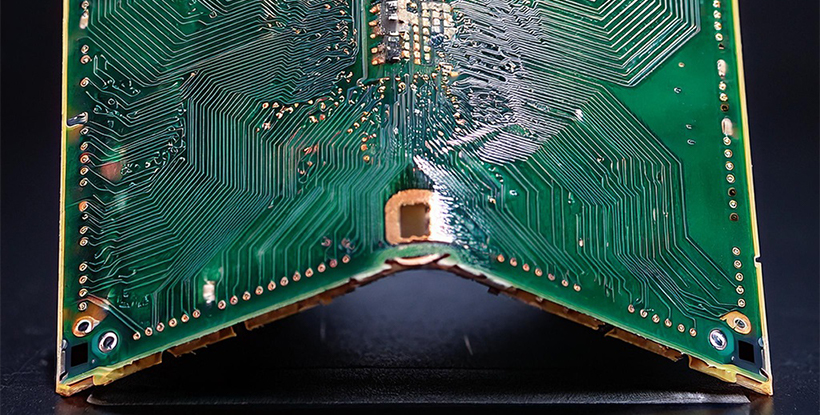
内部応力が発生する主な原因は以下の通りです。
2-1. 温度変化
SMT工程では、リフロー炉を使用してハンダを溶融させます。この際の急激な加熱と冷却により、基板や部品に熱応力が発生します。特に、異なる熱膨張係数を持つ材料が組み合わさる場合、応力が大きくなります。
2-2. 材料の選択不備
材料の物性や特性を十分に考慮せずに選定すると、応力が集中しやすくなります。例えば、柔軟性のない基板材料や、低強度のはんだ材を使用すると、長期的な問題の原因となります。
2-3. 設計上の問題
部品の配置やランドパターン設計が不適切だと、ストレスが集中する箇所が生じます。特に、大型部品や異形部品を使用する場合、その周辺に応力が蓄積されやすいです。
2-4. 製造プロセスの不適切さ
製造工程での不均一な温度分布や、はんだ量の不足・過剰による接合不良が応力の原因となります。また、部品装着時の圧力や振動も影響を及ぼします。
3. SMT製品に与える影響
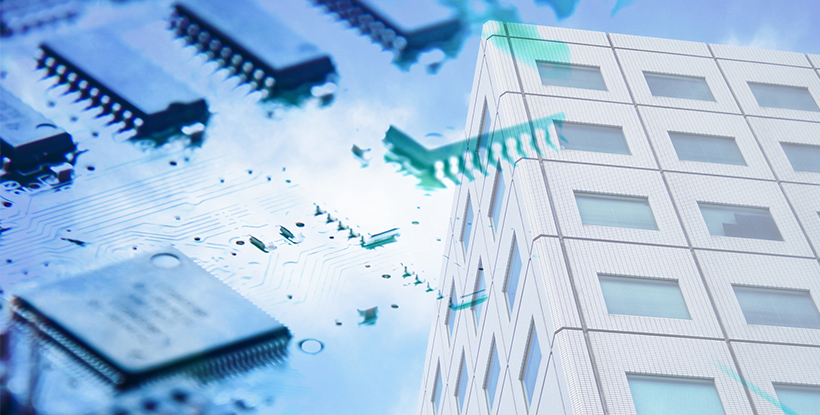
内部応力は、SMT製品の品質と信頼性に深刻な影響を及ぼします。具体的な影響は以下の通りです。
3-1. クラックの発生
応力が蓄積されることで、基板やはんだ接合部にクラックが発生します。これにより、回路が断線し製品が故障するリスクが高まります。
3-2. 接合部の劣化
内部応力が繰り返し作用すると、はんだ接合部に疲労が蓄積し、剥離や劣化が進行します。
3-3. 信頼性の低下
応力の影響で基板の反りや変形が生じ、製品全体の性能に悪影響を及ぼします。特に、過酷な環境下で使用される製品では、この問題が顕著です。
3-4. メンテナンスコストの増加
内部応力が原因で頻繁に故障が発生すると、修理や交換にかかるコストが増加します。これにより、製品のライフサイクルコストが上昇します。
4. 内部応力の対策と改善方法
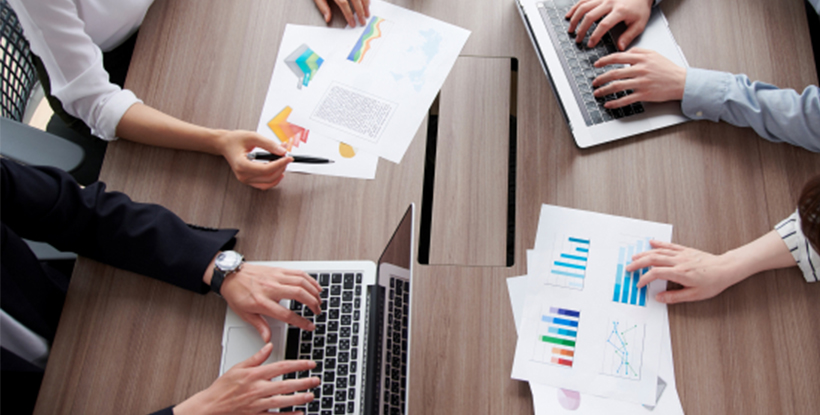
内部応力を最小限に抑え、SMT製品の信頼性を向上させるためには、以下のような対策が有効です。
4-1. 適切な材料選定
熱膨張係数が近い材料を使用することで、熱応力を抑えることができます。また、高強度で柔軟性のある基板材料やはんだ材を選ぶことも重要です。
4-2. 設計の最適化
部品配置の見直しや、応力が集中しにくいランドパターンの設計を行います。特に、大型部品を使用する場合は、その周辺に十分なスペースを確保することが推奨されます。
4-3. 製造プロセスの改善
リフロー工程での温度プロファイルを最適化し、急激な加熱や冷却を避けます。また、はんだ印刷や部品装着工程での精度向上も重要です。
4-4. 検査と評価の徹底
製品の応力分布を事前にシミュレーションし、応力が集中する箇所を特定します。その上で、X線検査や信頼性試験を通じて問題箇所を特定・改善します。
4-5. 教育とトレーニング
内部応力に関する知識を設計者や製造担当者に共有し、適切な設計・製造プロセスを徹底させることが重要です。
5. まとめ
内部応力は、SMTプロセスにおいてしばしば見過ごされる要因ですが、製品の信頼性や品質に重大な影響を及ぼします。その発生原因を理解し、適切な対策を講じることで、製品の性能向上とコスト削減が可能になります。内部応力を抑える取り組みは、短期的な利益だけでなく、長期的な製品価値の向上にも繋がります。設計・製造・検査の各段階での取り組みを強化し、より高品質な製品を市場に提供していくことが求められます。