1.実装検査の目的
SMT ラインの品質管理を行う際に、その指標の単位として「ppm(Parts Per Million):1 / 1,000,000」が用いられます。1970 年ごろは %(1 / 100)での管理が主流でした。工程内で品質を作りこみ、不良は作らないという考えのもとに、不良率を % でロット保証すればよかった時代で、品質保証は対象ロットの中からある数の製品を抜き取って検査し、その検査結果によってロットの品質を保証する、というものでした。ところが、技術革新とともにユーザーからの要求が高度化・多様化するにつれて、商品構造が複雑になると、部品点数の増加や IC の集積化が始まり、電子部品・自動車用部品などの不良率を 0.0001%(1 / 1,000,000) まで保証するようになりました。基板の部品点数が多くなり、さらには不良率を%で表すと 0.000001%のように 0 が続いてしまい、表記にも不便なため、現在では ppm という単位を用いることが多いようです。
%(パーセント)=1/100(百個に一個)
ppm(ピーピーエム)=1/1,000,000(百万個に一個)
2.不良率の算出
実装ラインの不良率を算出する際には、以下の 3 つの考え方を基準にします。また図 1のように、それぞれの特徴や実装における密度を踏まえながら、各々の実装検査で集計したデータをもとに不良率を算出していきます。算出は、図 2のような 3 つの方法があります。不良件数については、同一不良部品に異なる不良があれば、すべて不良とカウントします。
①基板 1 枚あたりの不良率
②実装点数(部品数)あたりの不良率
③接合点数(はんだ付け数)あたりの不良率
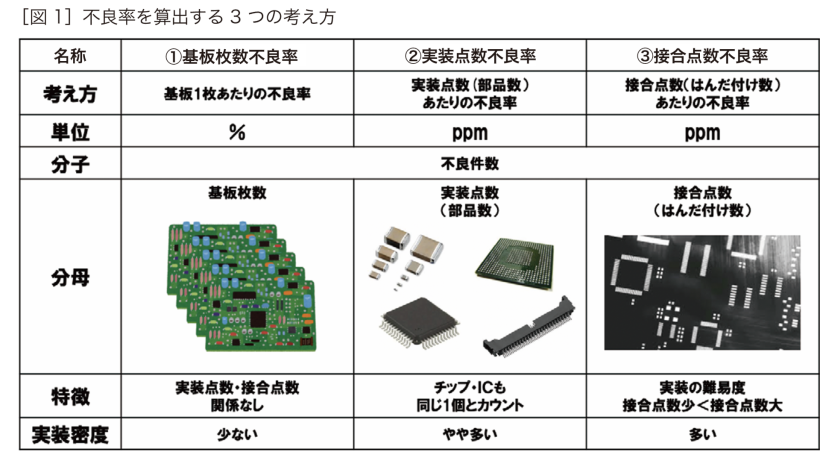
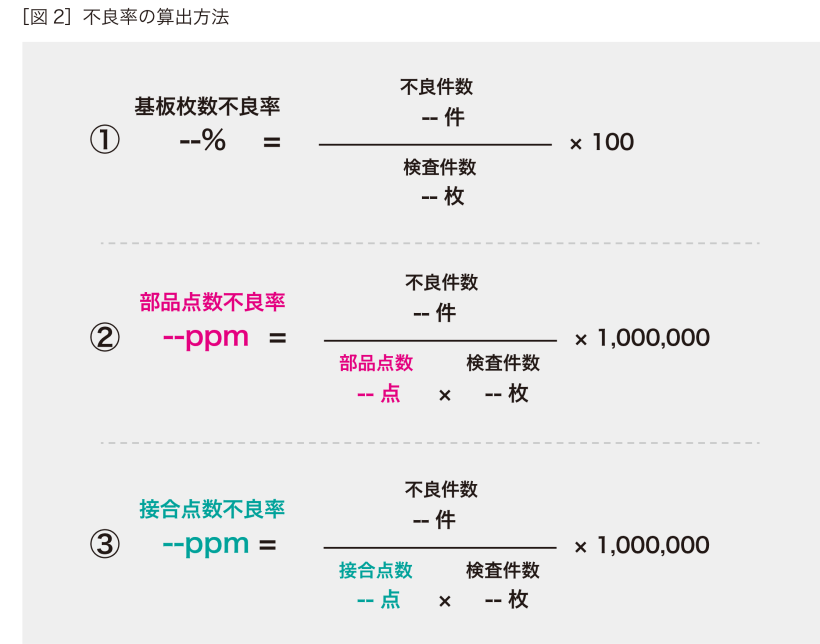
3.不良率の算出例
「検査枚数 100 枚、不良件数 5 件、実装部品点数 200 点/枚、はんだ付け接合点数 500 点 / 枚」の場合、不良率は以下のようになります。
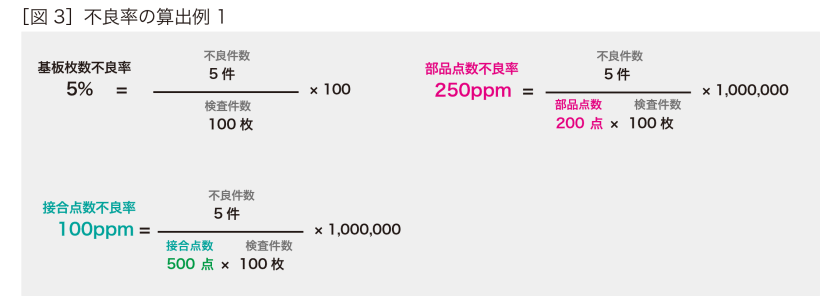
4.基板枚数不良率と部品点数不良率の違い
通常は、実装品質をより細かく把握するために、基板枚数不良率と部品点数不良率で日々管理していくことをお勧めします。例えば、下記のように A 社工場 -B ライン「不良件数 12 件、検査枚数 1,000 枚、実装部品点数 200 点/枚」と、A 社工場 -C ライン「不良件数 12 件、検査枚数 1,000 枚、実装部品点数 400 点/枚」で比較した場合、基板枚数不良率(%)は B ラインと C ライン共に同じになりますが、実装点数不良率(ppm)は異なります。
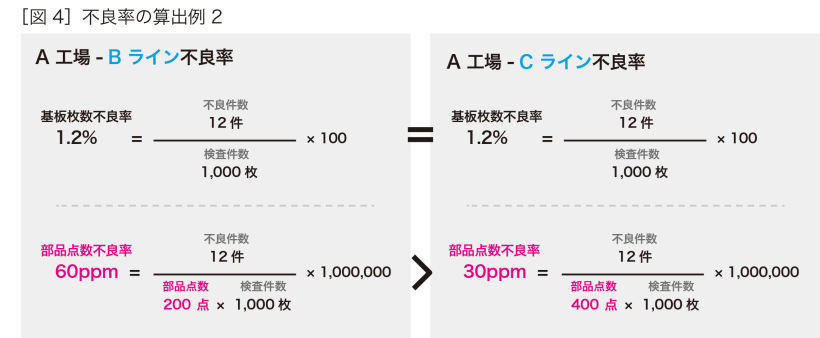
5.部品点数不良率と接合点数不良率の違い
同様に、不良率(ppm)でも部品点数不良率と接合点数不良率でも数字が異なりますので注意が必要です。例えば、下記のように A 社工場 -B ライン「不良件数 12 件、検査枚数 1,000 枚、実装部品点 数 200 点/枚、はんだ付け接合点数 2,000 点 / 枚」と、A 社工場 -C ライン「不良件数 12 件、検査枚数 1,000 枚、実装部品点数 400 点/枚、はんだ付け接合点数 1,000 点 / 枚」で比較した場合、部品点数不良率(ppm)は B ラインの方が、C ラインより高いですが、接合点数不良率(ppm)は C ラインの方が、B ラインより高い結果となります。以上のように、実装不良率と言っても、基板枚数、部品点数、接合点数のどれで見るのかによって、パフォーマンスが変わってきます。目的に合わせて、適切な KPI(key performance indicator )を設定する必要があります。
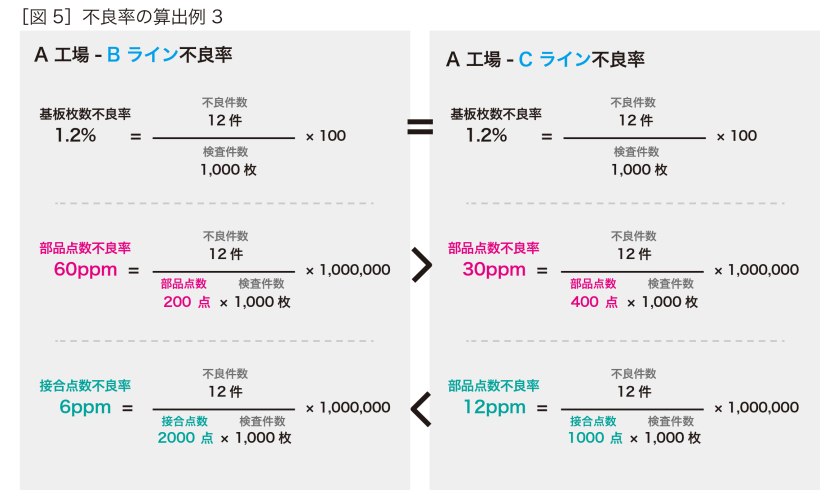
6.具体的な実装QCの進め方について
具体的な実装QCの進め方は以下「実装QCマニュアル」の資料をダウンロードしてください。OODAループの基本概念から実践まで分かり易くまとめています。こちらの資料に沿ってOODAを実施すれば現状把握から課題特定の方法、また仮説の立て方や検証方法まで正しく理解できます。是非ご覧ください。
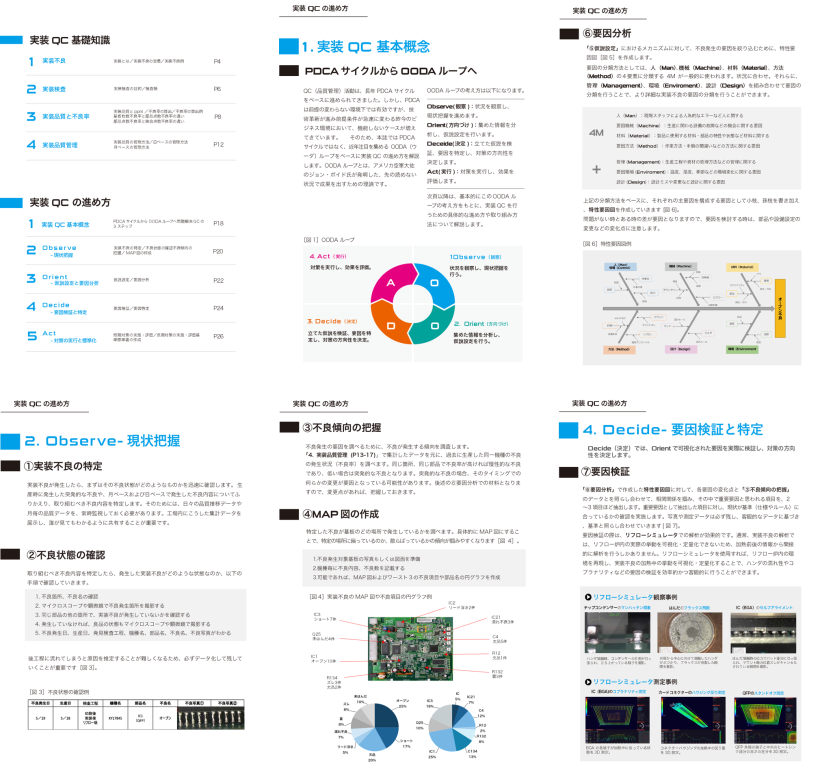